ネスティング作業
みなさんこんにちは、チームWTのTです。
最近、ネスティングを勉強し始めましたので、ご紹介しようと思います。
ネスティングとは板材料に製品を組み合わせていく作業になります。
作業をしている風景になります。
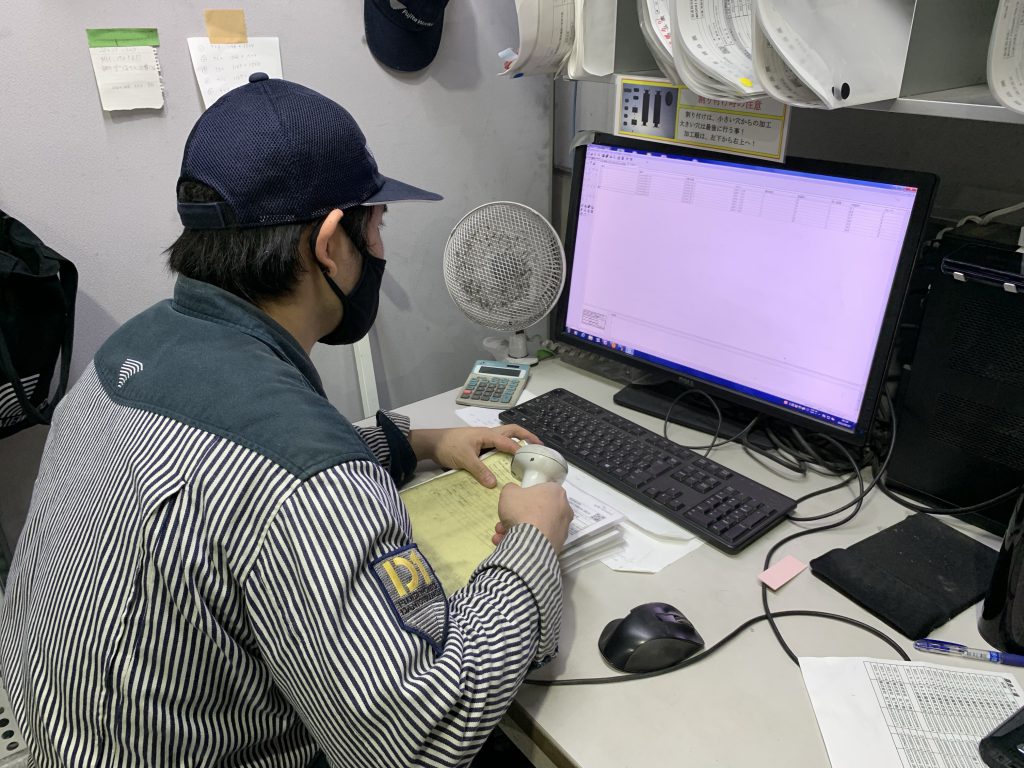
1つ1つ材料によって、色々な条件があったり、歩留まりを考えないといけなかったりとかなり頭を使いながら、日々取り組んでいます。
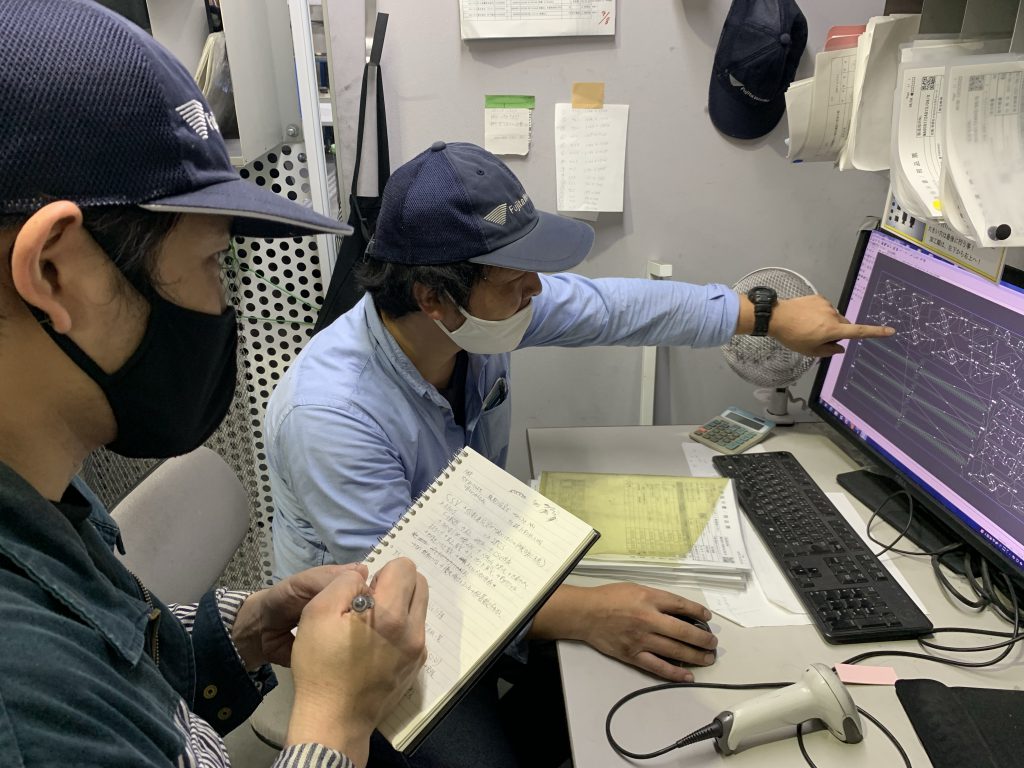
先輩に指導していただきながら、他の作業と並行して、自分自身スキルアップできるようにこれからも取り組んでいきたいと思います!
みなさんこんにちは、チームWTのTです。
最近、ネスティングを勉強し始めましたので、ご紹介しようと思います。
ネスティングとは板材料に製品を組み合わせていく作業になります。
作業をしている風景になります。
1つ1つ材料によって、色々な条件があったり、歩留まりを考えないといけなかったりとかなり頭を使いながら、日々取り組んでいます。
先輩に指導していただきながら、他の作業と並行して、自分自身スキルアップできるようにこれからも取り組んでいきたいと思います!
こんにちは。チームWTのSです。
今回はデンカイグループの依頼で製作した裏ガス治具について紹介させていただきます。
こちらが今まで使用していた治具になりますが、
・ガスの出る箇所が限られている
・溶接箇所にフィットしないため作業時に不安定である
といった課題がありました。
そこで溶接箇所にフィットしており、ガスが万遍なく排出される形状のものを設計しました。
スリットパーツ(図中青)に対して断面形状と同じ金属板を溶接するのに使用するため、
溶接する側にパンチングメタル(図中オレンジ)を配置することにしました。
こちらが完成した治具になります。イメージ通りの形状に仕上げることができました。
デンカイグループの方にも使用していただいたところ、仕上がりが良くなり、
裏ガス流量を減らすこともできたとのことでした。
治具を組み立てる際の溶接で失敗をしてしまい、再製作になってしまったので
溶接の技術を向上させることは勿論ですが、組み立て・溶接しやすい設計を
心掛けようと思いました。
こんにちは、チームさんさんのSです。
今回は、酸洗いのあげ作業について紹介していきたいと思います。(あげ作業とは洗浄・エアーブローの事です)
酸洗いは、焼け取り作業よりも後処理が不十分だとシミが出やすく時間がかかります。
しかも、酸洗いの製品は乾きやすく、すぐに水垢が出来てしまうのでスピード勝負の作業となります。
これからは製品のどこからシミがでやすいかなどを考え、スムーズに作業に入れる様にしていきたいです。
まだまだ暑い日が続いていますが皆さんいかがお過ごしでしょうか?
今回は1st stage(抜き工程)で行っておりますマルチ化についてご紹介します。
私は抜き工程で仕事をしておりますが抜き工程には複合機と単体機の2種類の設備があり、私は単体機を担当しています。
単体機はレーザーのみ、複合機はレーザーとパンチ加工、自動で材料をセットし加工した製品を棚まで持ち出し連続して加工が出来る為
長時間加工が可能です。その為、製品の材質、板厚、形状など様々な製品に対し最適な設備を選定して加工を行っています
弊社では1工程2名以上の育成という目標を掲げており人材育成に力を入れています
そこで私は複合機の教育を行っておりますがこれが難しい難しい……
普段単体機に慣れているのでパンチ加工の金型の種類や金型交換、プログラム上でチェックしたり、材料棚の操作やどこに何の材料があるかなど覚える事が多く一つのミスが大きな損失になりますのでプログラム入力後の確認など様々です
この様にマルチ化を推進する事で自身の能力向上、人員不足や不測の事態にも早急に対応出来る事で会社の為になるので引き続き頑張って行きたいと思います
また私自身も身に付けた事を若い後輩達に教育を行い技術・知識の継承を行って行きます
こんにちは
チームネッキーの担当のFです。
今回は、8/27に開催されました、夏休み恒例『FW家族参観』について書きたいと思います
毎年、FWではご家族を対象に、会社でのお父さん、お母さん、おじいちゃん、おばあちゃんが毎日どんな仕事をしているのかを実際その場に行き見学してもらっています。
去年はコロナのせいで開催できませんでしたが、今年は少しでも子供たちの夏休みの思い出になればと思い開催を決定しました
家族参観の内容を簡単に説明すると、まず初めに簡単な会社の説明
実際現場に行く(仕事見学)
親子板金教室(子供でも作れるような簡単な工作教室)を実施しました。
今年の工作教室はキラキラBOXを作りました
もちろんFWで考えた完全オリジナル作品です
準備する側からすれば試行錯誤を何回も繰り返しとても大変でした
が、、、出来上がった所を見ると本当にきれいで、いいものが作れたと思いました
こちらが見本の作品です
みんなとてもうまく作っていました
最後にみんなで記念撮影
コロナ禍で大変な時期ですが、少しでも楽しい思い出になったと思います
今年の家族参観も大成功でした🎉
こんにちは!チームRMのIです。
今回は現在ジョブローテーションで1st Stage の教育中のH君をご紹介をさせて頂きます!
H君は1st Stage で抜き工程2ヶ月目となります!
そんなH君は作業中の安全を意識して日々の業務に取り組んでいるみたいで、特に大きな製品等を扱う際は製品はもちろん周りの人や物に注意して慎重な作業を心がけているそうです!
新人作業者からは沢山の事を学べる機会ですので私もスキルアップを目指し頑張っていきたいです!
こんにちは、チームRMのKです。今回はスポット治具製作活動について紹介します。
スポット溶接では、製品を1度圧着してしまうと強い電流と圧力をかけ溶着するため取り外しが困難になり、位置ズレがとても致命的なミスになります。
それは溶接時手が触れた、製品が滑った等の些細なことでも起きてしまいます。
そのため仮付などがされていないものは、集中力と時間をつかい慎重に行う事になり、生産性も悪く不良の可能性にも繋がります。
そこで治具を使うと、ミスもほぼ出ず部品をはめ込んで打つだけなのでかかる時間が大きく短縮し、精神的にも楽でとても難易度が下がります。
スポットを始めて3ヶ月の私はまだまだ今までのプロセスにのっとって仕事を行うことが多いですが疑問や改善できそうなものは、積極的に提案し生産技術や設計の方々と協力してより生産性向上や不良を出さないようにすることに取り組んでいきたいと思います。
こんにちは!チームRMのFです。
前回設計途中であった塗装エリアに設置予定のブースですが、粉塵等の侵入を優先的に防ぎたいのは塗装を行う側(片側だけ)であったため一旦片方の面だけを設置して様子を見ることになりました。
前回同様にバラすことの想定はもちろんのこと、仕切りでは力不足であった場合ブースへの変更もあり得るため修正を考慮した設計で進めました。
角パイプ同士での溶接は何度か経験がありましたが、開口部と板金との溶接は初めてでブラケットも含めベースとなる板金にマーキングをしただけであったため溶接の際は苦労しました。
また、ベースに対して角パイプとブラケットを4枚、何箇所も溶接していたためベースの外周が上方向に反っておりプラスチックハンマーを使った歪みの取り方をグループ長に教わりながら実践しました。
歪みに対して反対方向に叩くときはある程度力を込めて、叩きすぎた時は加減をしながら叩く。
ここで力を入り戻しすぎるとぐにゃぐにゃになって歪みを悪化させてしまいます。
プラダンの中央部を支える受けの溶接自体は簡単に行きましたが、溶接歪みが酷く両端に角材を置いてその上で中央部に少しずつ体重をかけ歪みを和らげていきました。
塗装からあがり、組立に入りました。ものがそこまで大きくなければ組立終わってから設置するのですが、今回の場合そういう訳にはいかないため塗装エリアに道具を運んで組立を進めました。
局所排気装置の端に基準を設けて一番奥の柱の位置を決め先にアンカーボルトで固定しました。
次に隣の柱を立て水平軸のパイプをブラケットと共にボルトで固定を行いました。
今回は手前からボルト、バネ座金、平座金、ブラケット・角パイプを挟んでナットという形にしていましたが、本来緩み出すのはナットであるため、ナット側にバネ座金、平座金を入れるべきとのことです。ボルト側には平座金を挟み受ける面を広げて塗装の剥がれを抑えます。
一本目と二本目の柱間のねじ止めが終わったら、二本目の柱を固定するのではなく先に三本目の柱を立て前述同様にねじ止めを行いました。
角パイプとブラケットを全てねじ止めしきったら、柱の固定を行います。今回は水平度、平行度等を見ることのできる装置の操作を教わりながら縦柱の並行度を調整しました。二本目を先に固定しなかったのは並行度を合わせる作業を一度で済ませるためでした。
骨組み(角パイプ)の設置が終わり、パイプ間などの寸法を記録して3DCADにあるデータと比較して微調整を行いプラダンのカットサイズを決めていきました。
角パイプ間のプラダンのカットは単純でやり易いのですが、奥の柱と局所排気装置を繋ぐ壁には角度を調整できるカットの方法を調べて試作にて確認した上で実践してみました。簡単に言えば片面を残して肉を抜く作業なのですが、プラダンのサイズの関係上横向きで効果的に使うためには、プラダンの目に対して垂直方向にカットしなければならず、非常に大変な作業になりました。
しっかり納まるか不安であったため、角パイプ間のプラダンのカットが終わった段階で確認を行い問題なかったため固定していきました。ここではプラダンを角パイプと挟んで固定する板金部品において、一本の角パイプに2枚のプラダンが乗っかる部分をそれぞれ別の板金で固定しようと設計していましたが、ここは幅の広い板金を使うべきでした。
またドリルビスを扱う際、インパクトドリルの強さ調整をせずに作業を進めたためブラダンを押さえる板金パーツがいくつか変形してしまいました。
パイプ間のプラダンの設置が終わった時点で製作依頼者と話をした際、局所排気装置のスイッチが装置の側面についているからスイッチを触れる小窓が欲しいとのことでした。下見で寸法などをチェックしていた段階では存在に気付いていなかったのでカットの前に話を聞けたことはラッキーでした。
肉抜きカットを行った後に、小窓(簡易扉)の追加を進めました。
扉の切り抜きまでは順調だったのですが、幅的に横には開けないことに気付き下側に開く扉に決定しました。
作業を進めるにつれて問題点はいくつも発生し、何度も調整を繰り返して扉として作動することを確認できるまでになりました。
今回はこの部分をプラダンで製作していたからこそ扉の追加ができました。
設計を始める前の下見の時点で装置の側面にスイッチがあることを把握できていれば、この部分は板金で作った方が断然楽だったと思います。
今回も反省点は沢山ありましたがなんとか完成させることができたこと、この製作を振り返りながらブログで紹介することができて良かったです。
貴重な時間を割き、最後までお読みくださいましてありがとうございました。
こんにちは、チーム段のSNです。
現在、仕上げ工程の焼け取りの研修を行っているのは、新人社員のNさんです。
はじめは焼け取り箇所の見落としや、作業時間の掛かる製品などに苦戦しているようでしたが、研修開始から1ヶ月が経過し、徐々に慣れてきているように思います。
これからは、焼け取りの作業だけでなく扱う製品について知っておかなければならないことや、前工程・後工程についてもっと理解してもらえるように指導していけたらと思います。
焼け取り室の窓にブラインドを取り付けて頂きました。
特に朝の日差しはかなり眩しかったので、これで朝から快適に作業出来るようになりました。
こんにちは、チーム段のNです!
今回はジョブローテーションで下段取りに回ってきた新入社員のK君を紹介します!
下段取りに来て現在一ヶ月が経ち、主にエッジ取りと、メタルエステでの作業を教育しております!とても真面目に作業に取り組んでくれています!
下の写真はジョイントエッジと、メタルエステの設備の操作を指導している所です!
今後も下段取りでの作業を安全第一で教育していきたいと思います!