初投稿!
こんにちは!
チームうっちーやっしーのHです。
入社1年と5日目です、去年の今頃はバクバクの緊張と不安で入社してきました。
現在はとても楽しく作業を行っています。
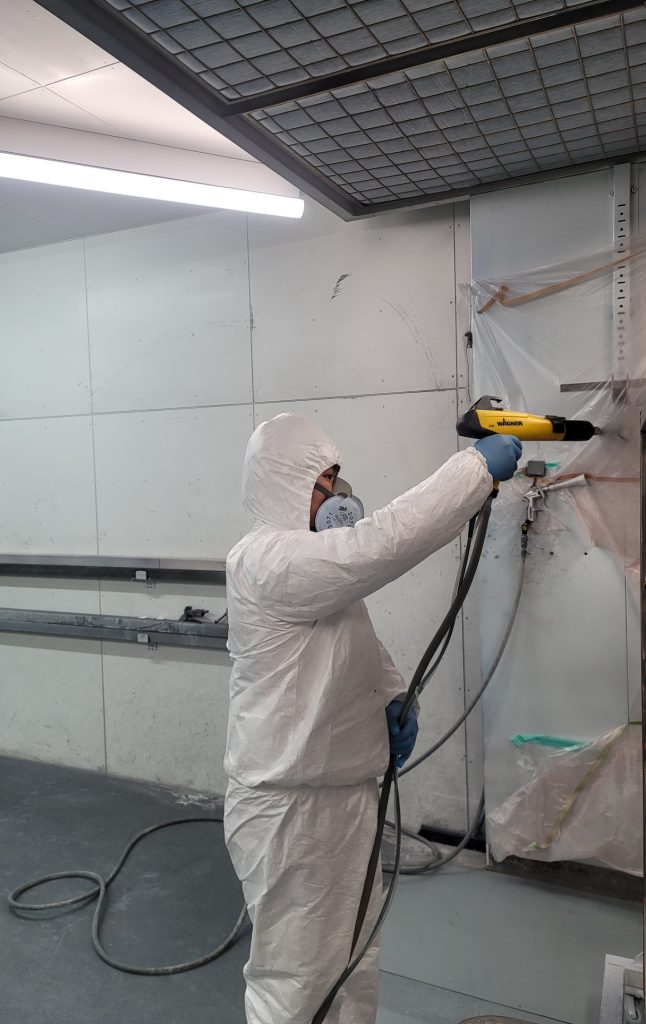
写真は初めて塗っているところです。
これからも楽しく頑張っていきたいと思います。
こんにちは!
チームうっちーやっしーのHです。
入社1年と5日目です、去年の今頃はバクバクの緊張と不安で入社してきました。
現在はとても楽しく作業を行っています。
写真は初めて塗っているところです。
これからも楽しく頑張っていきたいと思います。
こんにちは
チームうっちーやっしーのKです
4月に入り徐々に気温も上がり、過ごしやすい季節になってきましたが寒暖差が
まだまだありますので体調管理には気を付けていきましょう
今回は1ST STAGEグループの昼礼の様子をご紹介します
1ST STAGEグループグループでは朝礼、昼礼、17時にミーティングを行っております。
朝礼では、連絡事項や進捗状況、経営理念、品質方針の唱和をグループ員全員で行います。
昼礼と17時のミーティングでは、各設備の担当者が本日の進捗状況を伝えて、
負荷の高いところはないか確認します。
負荷の高いところがあれば、フォローできる人が入り、負荷の低減、残業削減に努めています。
1ST STAGEグループはなんといっても、抜群のチームワークです
2022年度もチーム一団となって頑張っていきます
おはようございます。代表の藤田です。
本日から2022年度がスタートしました。コロナ禍も収束しないままウクライナ危機が勃発し全世界の政治経済が不安定な状況の中で材料や一般消費財、エネルギーコスト高騰に歯止めがかからない状況です。
そんな中でも2021年度は売り上げ増を達成しそうです。これもひとえに、社員やBP様の努力と創意工夫の賜物だと心から感謝申し上げます。
2022年度は、新入社員を新たに迎え、さらなる成長を目指し皆さんと共に夢を実現できる藤田ワークスとなるようにチャレンジして参ります。
さて、今週日曜日がK工場長兼PGM(プロダクトゼネラルマネージャー)の誕生日でした。
FW入社32年目となり50歳を迎えました。おめでとうございます🍰🍾🎉💐。
Kさんにとって藤田ワークスは人生そのものだしKくんが藤田ワークスを成長させたと言っても過言ではありません!
お客さまもわざわざ遠方からお祝いに駆け付けてくださいました!
満面のKスマイルです。
50代も全力で頑張るそうです!期待しています。
桜の咲く今日この頃、すっかり春めいてきました。
先週末の風と雨でも負けないで花が残っています。
私事ですが昨夏より第1種衛生管理者の資格取得に向け取り組んでおりました。
1回目は8月、2回目は12月、3回目が2月でした。
1回目は鹿児島県で受けたので結果が出るまで1か月かかり、全体の50%で不合格。
ちなみに合格基準は、5科目の正答率40%、合計で60%以上となっています。
2回目は、福岡で受験し、結果は1週間ごにでましたが、あと一歩及ばず。
3度目の正直で2月22日とエンジェルナンバーの日に受験。
1週間後の発表で結果は合格しました。
58歳にして合格したのでとてもうれしかったです。
年のせいか記憶力も衰えている中、運がよかったと思います。
by あっきー
お疲れ様です!
今週のブログ担当のチームWTのMです。
自分が、ブログ投稿を担当してから一年が経とうとしています。
私はFCOグループに所属しており、曲げ加工を担当しておりますが、一年前と比べて加工速度は上がったため、
次のステップに進むために少し難易度が上がった製品を少しずつではありますが加工しているところです。
ですが超えるべき壁はまだまだたくさんあるので、一日でも早く先輩たちに追いつけるよう頑張っていく二年目にしたいです。
こんにちは
チームWTのMです。
私は、現在L曲げやハット曲げなどを加工していますが、
先日紹介したM君が今後加工していくにあたって、自分は箱曲げなどを加工していくことになっています
いきなり加工量産はできないため、空き時間で練習し今後のために備えています。
こんにちは。 チームWTのMです。 今回は現在私の所属するFCOグループで2月に配属になったM君をご紹介します!
M君はFCOグループでトルベンド7036で曲げ加工を行なっています。
今はL曲げを中心に、Z曲げハット曲げをの加工の練習も行ってます。 ケガがないよう、楽しく加工ができればと思っております。
こんにちは
チームさんさんのNです
今回は作業現場で使用する工具の点検を行いました
製品加工の際使用するグラインダーは加工時の粉塵が溜まり故障の原因となります
定期的な点検を行い不備があれば対処します
工具を大切に扱い少しでも長く使用できればと思います
こんにちは 🙂
チームさんさんのYです。
今回、生産技術グループのF君が作業台を製作して下さったので紹介致します。
こちらです
1月にFinalStageグループ(検査・梱包業務)に導入されたJUSTFITBOX(段ボール裁断機)用の作業台です。(作業台上で段ボールの接着を行います)
ベニヤ板、イレクターパイプ、藤田ワークス製の板金(引き出し)によって組み立てられています。
作業しやすい大きな天板と、マニュアルや筆記用具を保管できる引き出しがとても使いやすく非常に助かっています。
F君ありがとう。 😛
皆さんこんにちは~
チ-ムさんさんのURです。最近朝は寒く、日中は暖かい日があり春の訪れを感じますよね。
今年度も残りわずかではありますが頑張りましょう。Trumatic7000の教育を日々2時間程受けてきました。
すでにCランクぐらいあるのでは—-っと思える程扱える様になりました。
そこで今度はパイプ加工に挑戦しようとN先輩に弟子入りをしました。
今年は新しい設備が入ってきます。少しでも力になれる様、今からパイプ加工の知識と技量を身に付けたいと思います。
今回のブログで最後になります。次回は新しいブログ担当者になります。2年間有り難うございました。