工夫改善(スヌープ試験台座)
皆さんこんにちは😃
今回は社内で行われている工夫改善活動の一環で製作したものについてご紹介したいと思います☝️
社内では溶接作業後の漏れ検査としてリークチェック(スヌープ試験)を行なっているのですが、その際に使用している試験機材を置く台座を生産技術グループの方にご協力頂き製作しました。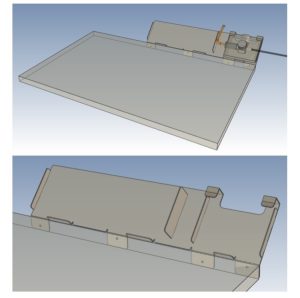
この台座に置けば作業台から機材が転落する恐れも解消できる為とても助かっています。
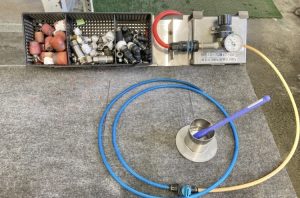
また固定した状態から簡単に脱着もできる構造になっている為、持ち運びする際にも便利です✨
引き続き日々様々な工夫改善(考え、行動し、展開する)を実践して、品質や生産性を高めていけるよう精進して参りたいと思います😊
チームFW F
二刀流、頑張ってます✨
おはようございます
チームRMのkです😊
気づけば、ブログ担当2年目も次回で最後の投稿!今までは接着のお仕事についてお話することが多かったのですが、今回は今年から少しずつ進めてきたマルチ化についてお話します
私の所属するグループでは接着工程以外にも組立に関する工程があり、現在の私はコーキングの作業を主に行っています✨
接着工程を後輩に引き継ぎながらの、新しい作業は苦労も多いですが
自分のスキルアップとグループのマルチ化に貢献できれば!と思い、二刀流、頑張っております
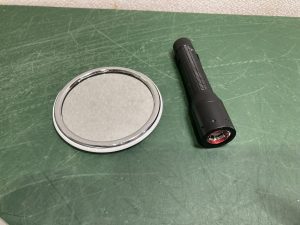
写真は、コーキング作業を始めてから頻繁に使うようになった道具。鏡とライトです
コーキング作業では、シリコンが溶接箇所等に隙間や穴がなく塗られていて水漏れが起こらないことが重要です
そのため、肉眼のみならず、見えにくいところは鏡とライトを使ってしっかり確認します
まだまだ修行中なので、もっと戦力になれるよう頑張ります🔥🔥
こんにちは
皆さんこんにちは!!
チームうっちーやっしーのHです。
以前よりも何個か塗料が増えました!
メタリック塗装は、難しく塗る間隔が大事です。メタリックが線のようにたまりやすくはだを出すのが難しい色です。
難しい色や製品、まだ塗れない色等があるので塗りの練習をし、早く塗れるよう頑張って行きたいです。
最近寒くなってきました、体調管理に気をつけて頑張っていきましょう。
板金教室
梅雨真っ只中、蒸し暑い日が続きますが
如何お過ごしでしょうか
チームWTの19です。
先月より、社内にて板金教室が始まりました。
業務以外で物を作りたい希望者が集い、各々で1つの作品を完成させるというものです。
数年前にも一度開催された事があり、私は2度目の参加になります( ᎔˘꒳˘᎔)
こちらは以前製作した棚です
(諸事情により部分写真ですみません)
暗くて分かりづらいですが、棚板の位置を調整出来る仕様になっています。
PCで一から作図し、物に依っては溶接や組立など普段携わる事がない工程を体験する事が出来るので、これからの仕事に繋げられる大変良い機会だと思っています。
以前は本棚を製作し、今回はシューズラックに挑戦中です。只今ご指導を頂きながらPCにて作図に取り組んでます。
どんな出来栄えになるかは次の当番時にて。
お楽しみに!(笑)
メタルグリップ!!
皆さんこんにちは!
チームうっちーやっしーのKです💕
気温が少しづつ上がって来て夏が近づいてきたなと感じてきました😄
今回は、接着の中のメタルグリップについて話して行こうと思います!!
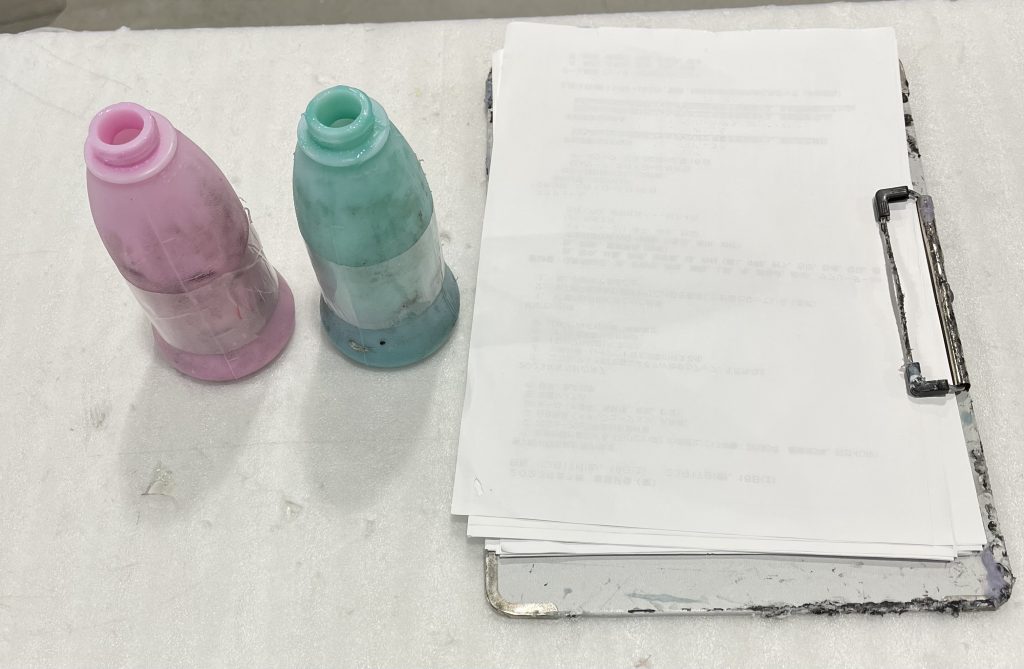
メタルグリップは、2つの有機溶剤を混ぜて接着する方法です!
他の有機溶剤は板金とゴムを貼ることが多いけれど、このメタルグリップは板金と板金を接着するためとっても強力で、1度くっついてしまうと取り外すのが難しいです💦
今は、小さい部品を貼ったり、マスキングテープを貼ったりするなどの準備を主にやってます
様々な形の部品があったり、溶接があるかないかで接着の仕方が違うので少しずつ覚えて接着ができるように頑張りたいです💕
久しぶりの投稿!
こんにちは!
チームうっちーやっしーのHです。
初めは溶剤塗装はとても難しく垂れたり、スケたりしていました、先輩に塗り方を教えてもらい練習をし塗り方が分かってきました!
下の写真・・初めて塗った時の写真と現在!
今は色んな製品を塗らしてもらい少しずつですが塗れる製品が増えてきました!
まだ塗れない製品があるので頑張っていきたいです。
設備紹介
初めましてチームうっちーやっしーのKです。
1stグループに配属されてから4ヶ月になり、現在はTruLaser3040という機械で板金の抜き工程を任されています。
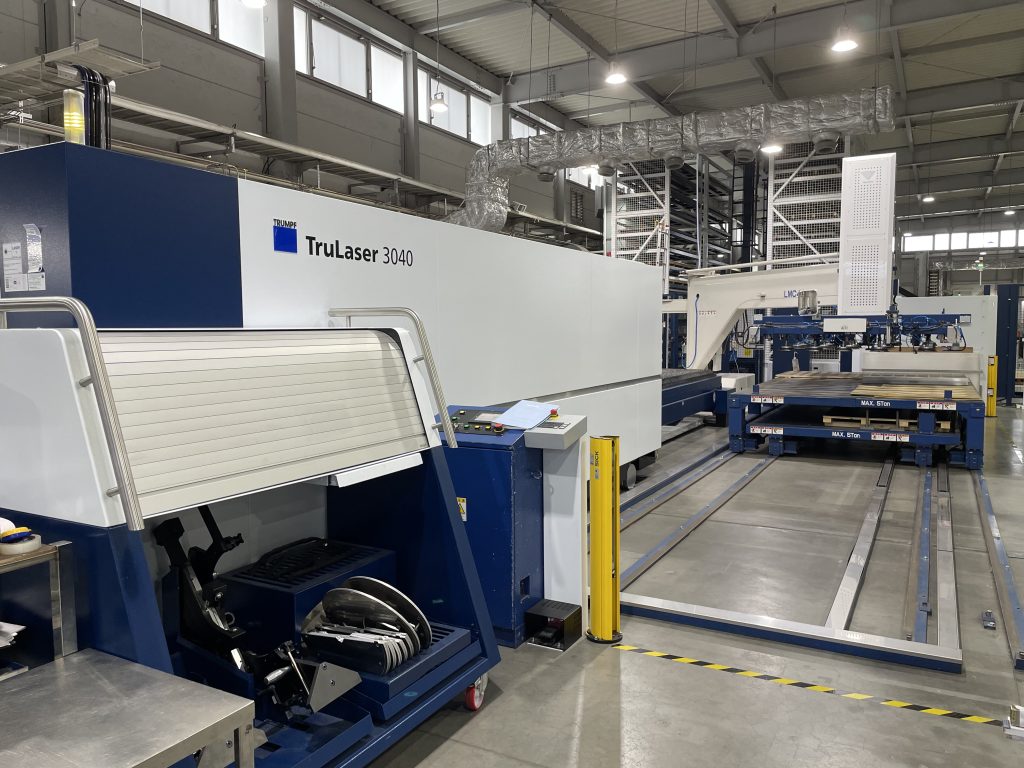
TruLaser3040は、名前にもあるようにレーザーで板金を切断する機械で、2023年の2月に導入されたばかりです。
この機械は薄板の切断を得意としていますが、25mmの厚板も加工することが出来ます。
導入されたばかりの機械ですが、うまく使いこなせるよう勉強しながら頑張ります。
初ブログ!!
初めましてチームうっちーやっしーのKです!
PーAに配属されてから4ヶ月になり、現在は接着をメインでやってます😊
今回のブログでは、接着について書いていこうと思います(*^^*)

最近は接着についての記録を取るようにし、自分がいつできるようになったのか、タイムがどれだけ縮まったのかが、すぐに分かるようにするためです!!
この記録を取る事によって、どのような段階を踏んで上手に出来るようになるのかを理解することが出来、新人の教育の時に、自分が難しくてできないポイントを伝えることが出来ます😊
接着を行って、まだ4ヶ月しか経ってないので、様々な製品に触れて、少しずつ成長できるよう頑張ります!!
台車扉の設計
こんにちは、チームWTのSです。
今回は最近製作した台車扉について紹介します。
依頼内容としては治具台車の飛び出し防止とホコリ対策を行いたいというものでした。
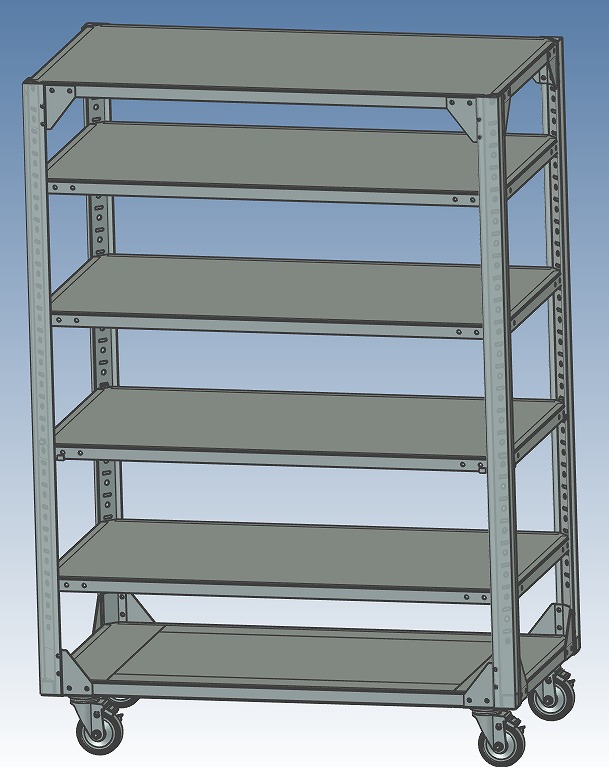
初めはロールスクリーンを設置すれば良いのではとも考えましたが、
良いサイズのものが無く、また飛び出し防止への抑止効果は薄いということで断念しました。
設計を始めてまず横の飛び出しに関しては横板を既存の穴で共締めすれば問題ないということ
ですんなり決まりました。
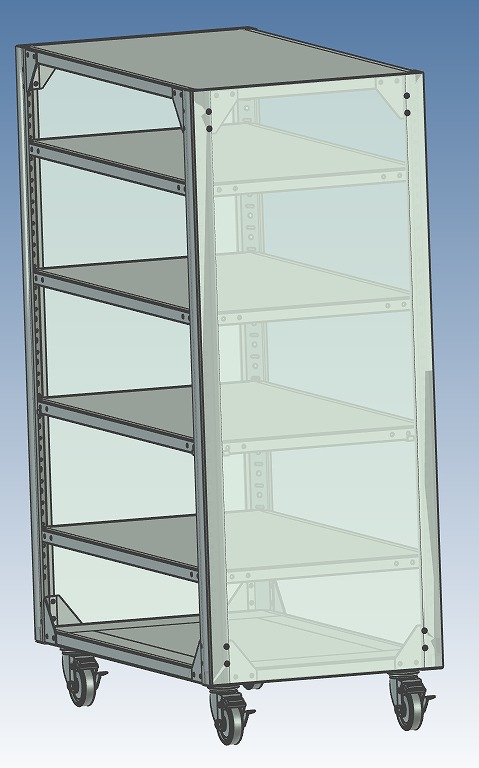
続いて正面の扉を設計する段階になり、台車に直接取り付ける場合、既存の穴だけでは足りず、
新たに穴を開ける必要があると想定されました。できればそれは避けたいので、枠になるものを
先に取り付けた上で扉の取り付けを行う方向にしようと思いました。
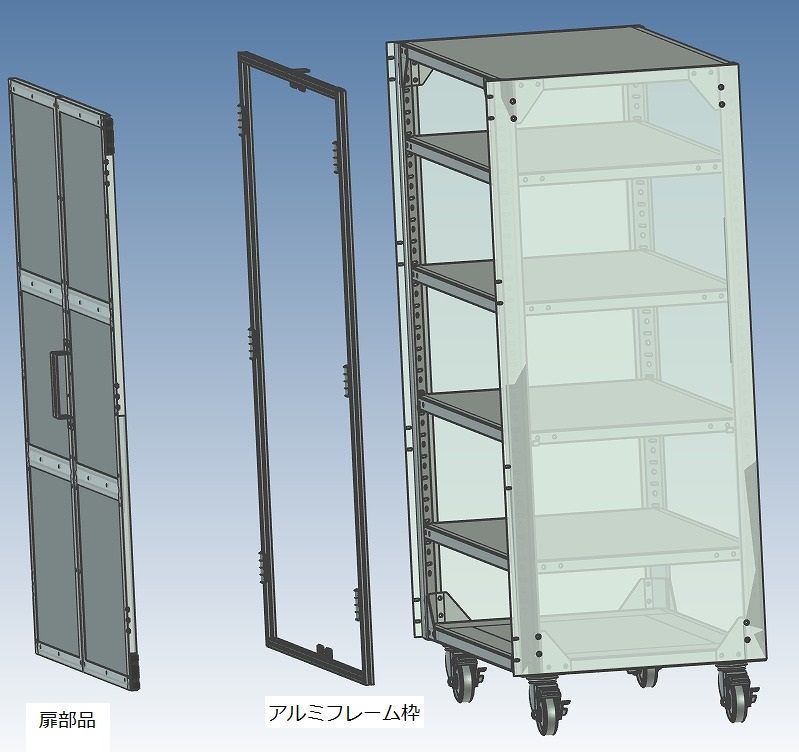
最終的に組立も容易で扉の取り付けでも位置の融通が利くアルミフレームを枠として
取り付けることにしました。横板をアルミフレームの幅だけ延長しボルトで固定(下左図)、
また台車本体とはブラケット(下右図・黒パーツ)で固定することにしました。
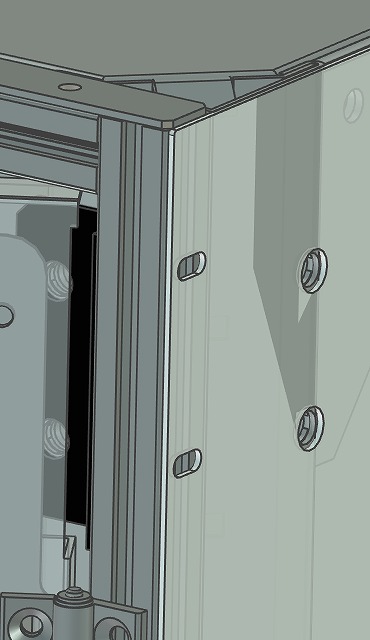
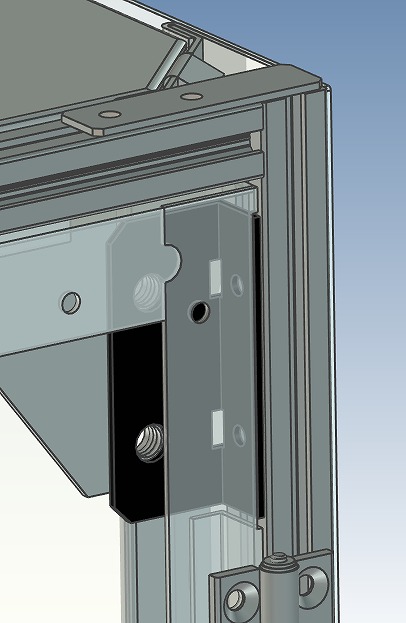
扉本体の設計に関しては、当初アクリルパネルをはめ込む予定でしたが、
中が見えなくてもよいとのことでしたので1mmのアルミ板に変更して、
軽量化することにしました。
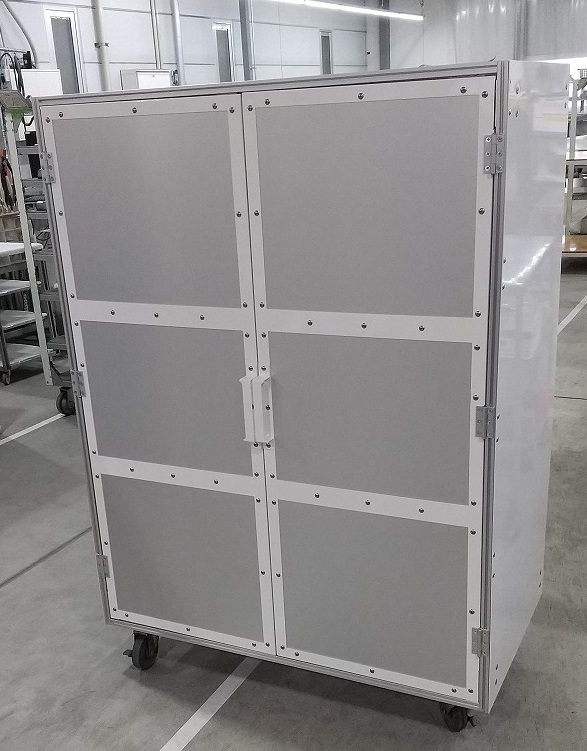
こちらが完成品になります。無事に完成しましたが、取り付けの際に
既に台車に取り付けてあるボルトがロックナットで固定されており、
外すのに一苦労したので、作業前にそういった条件も確認が
必要だと学びました。
今回のブログで担当が最後になります。2年間有り難うございました。
日々成長!!
こんにちは
チームさんさんのNです。
新入社員としてジョブローテーションを回り、
今のグループに配属が決まってから1年が経ちました
私はSFグループに配属になり、設計業務に就くことになりました!設計を始めてから2か月が経ち、少しずつCADの使い方にも慣れてきました。
現在は抜き直しの登録や板物や曲げ物の作図のみですが、
これからは溶接製品の作図であったり、指示書の工程を組む作業にも取り掛かると思うので
少しでも早く覚えられるよう頑張ります
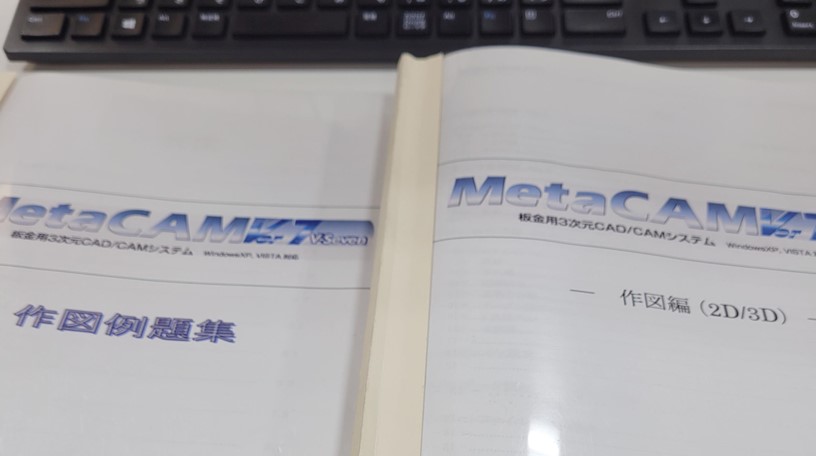