試験治具について
こんにちは、チーム段のSNです。
今回は仕上げ工程内で行う試験から、治具の紹介をしたいと思います。
試験では、溶接部に直接エアーを当てて漏れがないか確認するスヌープ試験、浸透液と現像剤を使用するカラーチェックなど、いくつかの方法があります。
その中でも加圧試験という方法では、製品を密閉して中の空洞に圧をかけるものですが、しっかりと密閉するには治具を使う必要があります。
こちらは筒状の製品に対し、両側からゴム性の蓋で穴を塞ぐことにより密閉できるという治具です。
こちらは筒の大きさに合わせて手前の赤いレバー部分を前後させることで、形の違う製品にも対応できる治具です。
このような治具を製作してくださる生産技術の方に感謝して、業務を行なっていきたいと思います。
PC周り改善
こんにちは 😛
チームさんさんのYです。
今回は、作業台に置いているPC周りを改善しましたので紹介します。
以前はモニター前のキーボードが作業スペースを圧迫し、作業の邪魔になる事がしばしばありました。
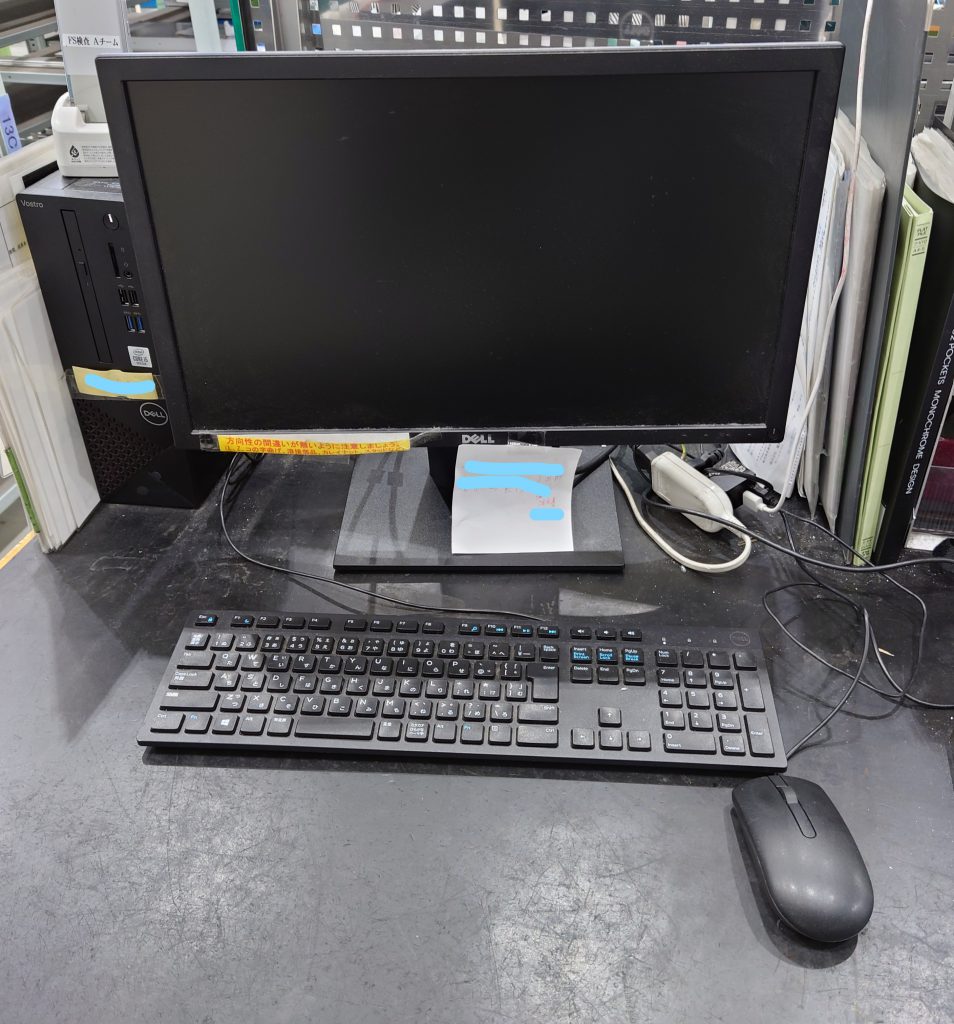
そこで
モニター台を製作し、キーボードを台下に収納する事にしました。
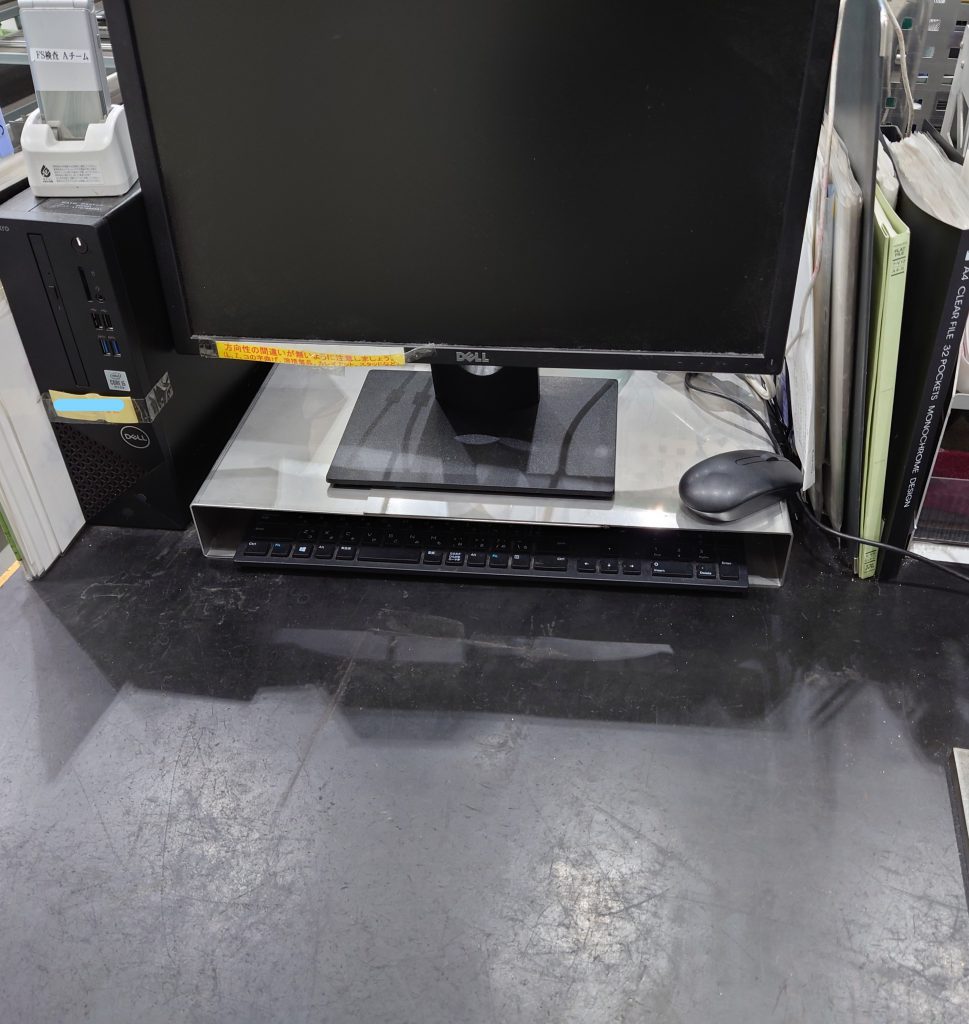
キーボードを使用時以外は台下に収納しておくことで、モニター前のスペースが広がりとても快適になりました 😛
これからも、作業が快適になるような改善を続けていこうと思います 😆
ネスティング作業
みなさんこんにちは、チームWTのTです。
最近、ネスティングを勉強し始めましたので、ご紹介しようと思います。
ネスティングとは板材料に製品を組み合わせていく作業になります。
作業をしている風景になります。
1つ1つ材料によって、色々な条件があったり、歩留まりを考えないといけなかったりとかなり頭を使いながら、日々取り組んでいます。
先輩に指導していただきながら、他の作業と並行して、自分自身スキルアップできるようにこれからも取り組んでいきたいと思います!
裏ガス治具の製作
こんにちは。チームWTのSです。
今回はデンカイグループの依頼で製作した裏ガス治具について紹介させていただきます。
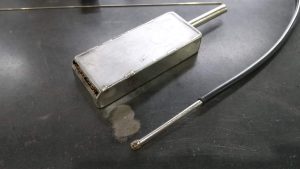
こちらが今まで使用していた治具になりますが、
・ガスの出る箇所が限られている
・溶接箇所にフィットしないため作業時に不安定である
といった課題がありました。
そこで溶接箇所にフィットしており、ガスが万遍なく排出される形状のものを設計しました。
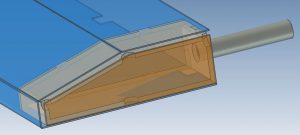
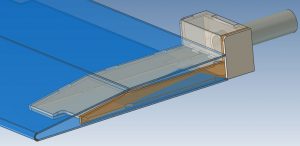
スリットパーツ(図中青)に対して断面形状と同じ金属板を溶接するのに使用するため、
溶接する側にパンチングメタル(図中オレンジ)を配置することにしました。
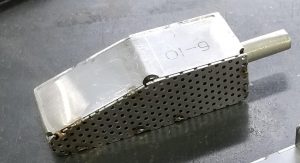
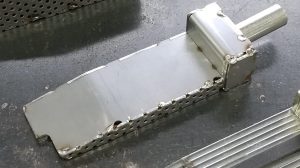
こちらが完成した治具になります。イメージ通りの形状に仕上げることができました。
デンカイグループの方にも使用していただいたところ、仕上がりが良くなり、
裏ガス流量を減らすこともできたとのことでした。
治具を組み立てる際の溶接で失敗をしてしまい、再製作になってしまったので
溶接の技術を向上させることは勿論ですが、組み立て・溶接しやすい設計を
心掛けようと思いました。
酸洗い作業
こんにちは、チームさんさんのSです。
今回は、酸洗いのあげ作業について紹介していきたいと思います。(あげ作業とは洗浄・エアーブローの事です)
酸洗いは、焼け取り作業よりも後処理が不十分だとシミが出やすく時間がかかります。
しかも、酸洗いの製品は乾きやすく、すぐに水垢が出来てしまうのでスピード勝負の作業となります。
これからは製品のどこからシミがでやすいかなどを考え、スムーズに作業に入れる様にしていきたいです。
社内改善物件のご紹介
こんにちは
チーム段のSです。
本日は社内の改善物件のご紹介をします。
弊社では最近、鉄道関係のN社さん向けの製品制作をさせて頂いているのですが、
大きな製品でとても部品点数が多く、自分達の工程の完成後製品管理をどうするか?
また、次の工程の加工前仕分けも時間がかかるという問題が発生していました。
そこで、今回、N社向け製品仕分け用兼工程内大物製品仮置き台車を制作致しました。
大きな台車が2台あるので、部品点数の多い製品も仕分けられるようになりました。
また、N社向け製品がない時は大きな製品や長い製品の仮置き、加工前のシール剥がし脱脂などの仮置きなど工程内の色々な作業がとてもやりやすくなりました。
改善はちょっとしたひらめきで作業がやりやすくなったり、楽になったりと、とても大事だと思うので、これからもいろいろ改善していこうと思います。
製品の傷直し
こんにちは
チームさんさんのNです
今回は製品の傷直しについて説明します
加工方法によって傷への対応が変わってきますが今回は下記の
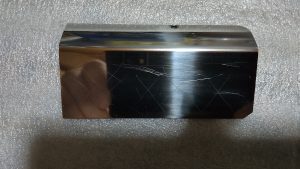
こちらの研磨加工の製品の傷直しを行います
よく見ていただくと浅い傷が多数ありますが
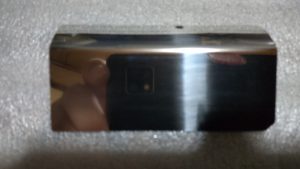
麻バフで磨き直すことで傷を消すことができました
センサーの埋め込み
こんにちは。チームWTのSです。
今回は最近の改善で板金部品と3Dプリンターで成形した部品を合わせて使用した事例を紹介させていただきます。
1stエリアのタッピングマシンの改善の際に、ワークを置くステージにセンサーを埋め込む必要がありました。
下図左が実際埋め込んだ画像になりますが、ステージ下が限られたスペース(下図右)であったため、
センサーを固定するにはどういう仕組みにすれば良いか悩みました。
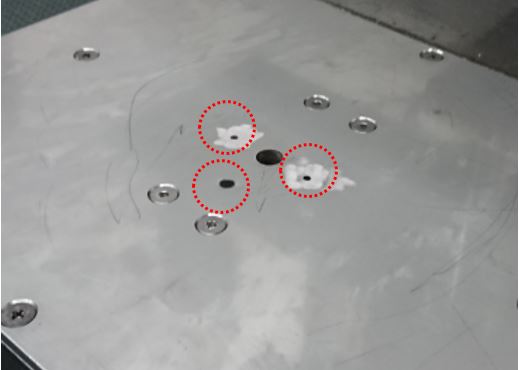
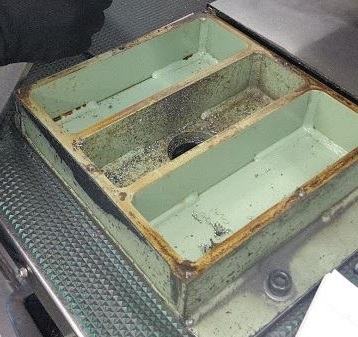
スペースに合わせて厚板を足し、側面から穴を開けてねじ止めする、という方針にしたものの、
センサーの口径が小さく加工できないことが分かりました。
そこで大きめの穴を開けて隙間を埋めるスペーサーを3Dプリンターで成形することにしました。
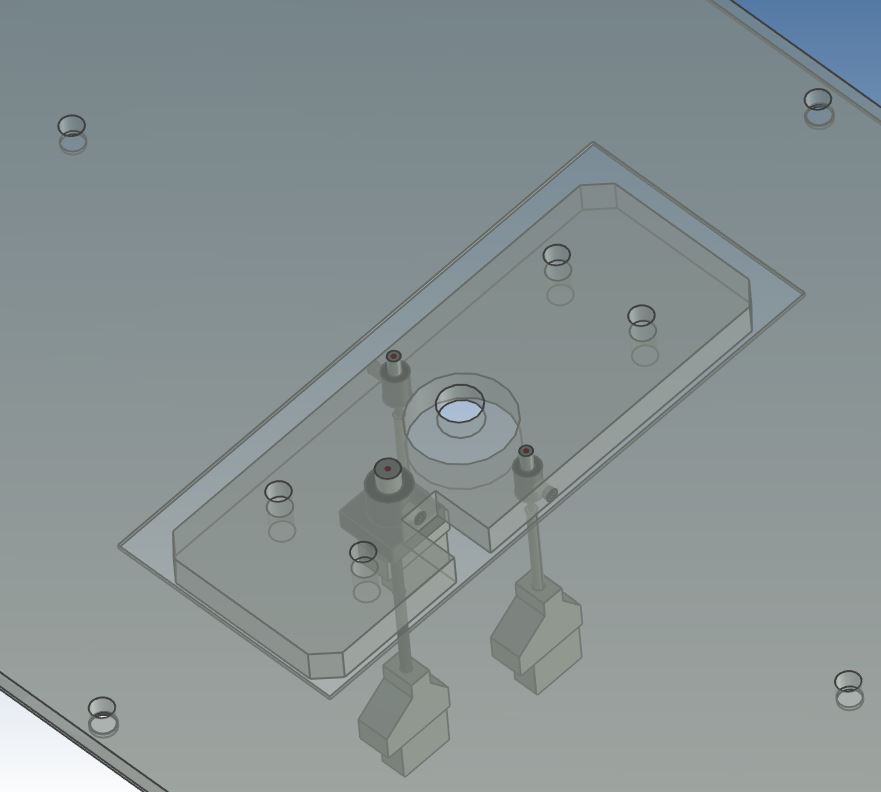
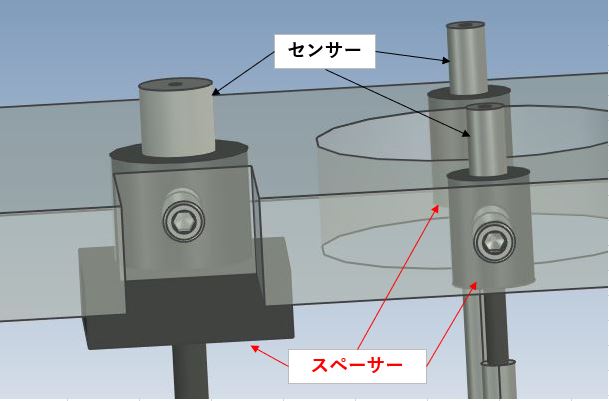
こちらが実際に成形したスペーサーを入れた図になります。
センサーをしっかり固定することはできましたが、センサーに合わせてスペーサーを
削ったりもしたので、今後の横展開に備えてもっとシンプルな構造にできるように
設計の引き出しを増やしていきたいです。
仕上げ工程
こんにちは!チームさんさんのSです!
今回は仕上げ工程で使われるMeister2について紹介します。
この機械では、回転しているペーパーを上から手で抑え、下にある製品を加工する作業に使われます。
HL仕上げでは製品に対して真っ直ぐ平行にかけなければならないのですごく集中する作業になります。
力加減や当たる位置、平行を常に意識しながらの作業になるので注意して作業する必要があります。
自分はまだHL加工には慣れていないので、これから効率よくきれいに仕上げられるように努力していきたいです。
浸透探傷試験
こんにちは、チーム段のSNです。
浸透探傷試験について、少しご紹介させていただきます。
ここで行っている浸透探傷試験とは、製品の溶接されている部分に穴や割れ、溶接ズレ等がないかをチェックする為の試験です。
まず、赤色の浸透液を溶接箇所に塗り、一定時間経過してからその部分を拭き取り、その後現像剤を吹き掛けます。
穴があった場合にはそこだけ赤色の液が漏れているので、欠陥が分かるという訳です。
今回は実際に、テストピースを用いて試験を行いました。
写真のようにNGとなると、その箇所を溶接をしてもらい、再度試験をして問題が無いか確認します。
こういった欠陥を見落としてしまうと、単にその製品が不具合品となるばかりでなく、製品が流れた先で重大な事故を引き起こしてしまう危険性もあります。
私は浸透探傷試験の作業についてまだまだ駆け出しですので、責任感を持って注意深く作業を行いたいと思います。